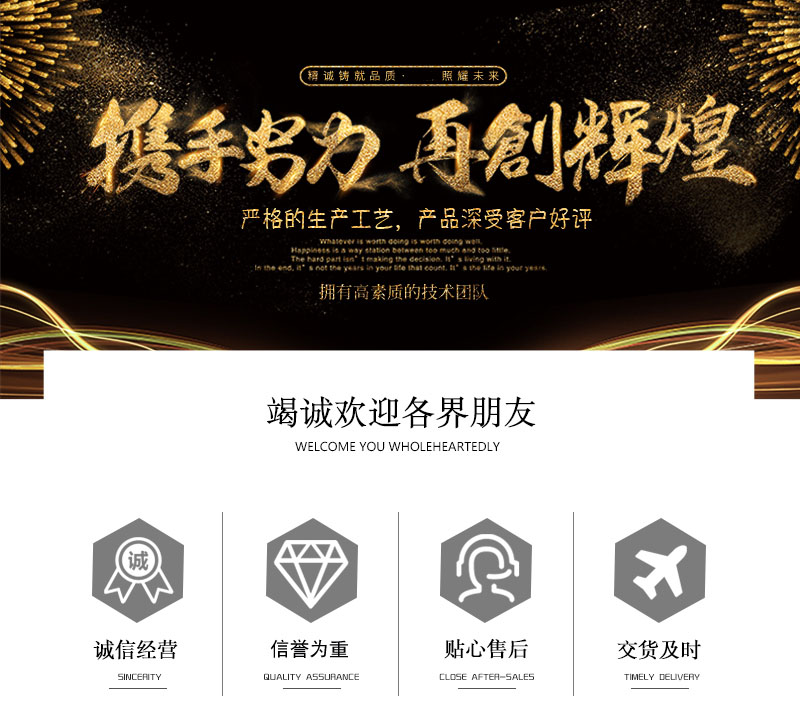

![]() | ![]() |
![]() | ![]() |
滾塑具射出成型的操作條件
1、背壓螺桿在旋轉加料時后退之阻力稱為背壓。其作用使原料在輸送壓縮中加緊密。能使原料的空氣,水份從螺桿后排出。使溶膠中不含影響成品表面的氣體成份。低會有氣泡,表面銀紋。高會過熱,結塊,溢膠,周期長,螺桿不退。同時松退的應用很重要:背壓低時,有的原料要松退,有的則不必(根據各種不同性質之原料調不止背壓)。背壓高時務必用松退并注意距離要不介入空氣及不溢膠為準則。
2、壓力和速度有部分相同的關系作用于滾塑模具內。目的使原料進入模內能均勻, 適量的充滿各角落。太低會短射,縮水,太高有毛頭,過飽,粘模,燒焦,易損模具及內應力高等不良現象
3、關模壓:原則上應大于塑膠射入滾塑模具內的總壓,以不出毛邊為基準
4、溫度:原料不同,溫度各異,太低溶液膠顏色不均,成品內應力增大。因溫度過低增壓過高,可能引起螺桿斷裂,過高,產品有毛邊,又因冷卻產生溫差,引起收縮。原料會分解,變黃,變色,易斷裂。冷卻時間變長,氣不容易排出,會有瓦斯氣。
5、速度:速度的快慢決定原料在滾塑模具澆道內及成品中之狀況,快有毛邊,過飽,燒焦,慢了出現短射,縮水,結合不良易斷等
6、模溫高低及冷卻時間的長短,影響成品的粘模,縮水,尺寸公差,表面亮度,周期等,應依實際際情況而適時調整。另壓克力,PC如成品肉厚時要有模溫,才不會產生氣泡及應力。
滾塑模具設計制作
滾塑模具設計制作的要求是:尺寸 、表面光潔;結構合理、生產、易于自動化;制造容易、、成本低;設計符合工藝需要,經濟合理。
滾塑模具結構設計和參數選擇須考慮剛性、導向性、卸料機構、定位方法、間隙大小等因素。模具上的易損件應容易 換。對于塑料模和壓鑄模,還需要考慮合理的澆注系統(tǒng)、熔融塑料或金屬流動狀態(tài)、進入型腔的位置與方向。為了提高生產率、減少流道澆注損失,可采用多型腔模具,在一模具內能同時完成多個相同或不同的制品。在大批量生產中應采用 、、高壽命的模具。
滾塑模具制造按結構特點,分為平面的沖裁模和具有空間的型腔模。沖裁模利用凸模與凹模的尺寸 配合,有的甚至是無間隙配合。其他鍛模如冷擠壓模、壓鑄模、粉末冶金模、塑料模、橡膠模等都屬于型腔模,用于成形立體形狀的工件。型腔模在長、寬、高 3個方向都有尺寸要求,形狀復雜,制造困難。模具生產一般為單件、小批生產,制造要求嚴格、多采用的加工設備和測量裝置。
平面沖裁模可用電火花加工初成形,再用成形磨削,坐標磨削等方法進一步提。成形磨削可用光學投影曲線磨床,或帶有縮仿、修打砂輪機構的平面磨床,也可在平面磨床上采用成形磨削工具磨削。坐標磨床可用于模具的定位,以孔徑和孔距。也可用計算機數控(CNC)連續(xù)軌跡坐標磨床磨削任何曲線形狀的凸模和凹模。型腔模多用仿形銑床加工、電火花加工和電解加工。將仿形銑加工與數控聯合應用和在電火花加工中增加三向平動頭裝置,都可提高型腔的加工質量。電解加工中增加充氣電解可提高生產效率。
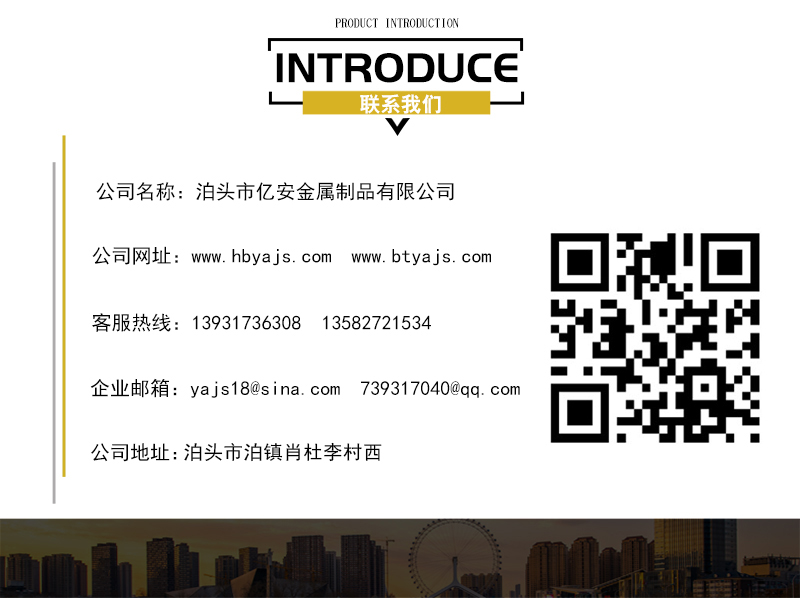